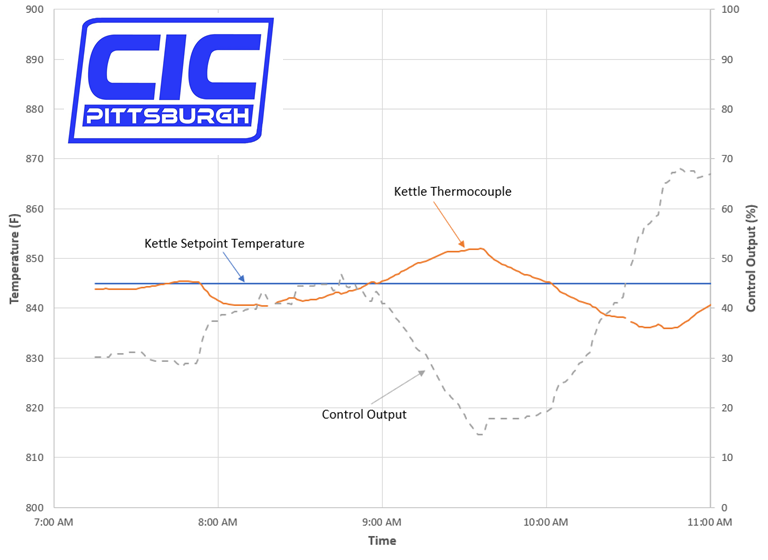
Maintaining zinc bath temperature control in the Hot Dip #Galvanizing process is not easy. While the temperature setpoint for the zinc in the kettle is steady, everything else in the process varies greatly, including batch sizes and weights, dip times and frequencies.
PID Loop controllers, with some advanced features, are the most common means for maintaining the bath temperature. PID stands for Proportional, Integral, and Derivative, which are the three contributing terms to the controller’s decision of how much to change the control output (heating rate) is to be used to match the desired bath temperature. The Proportional term applies a multiplier on the change in temperature error. The Integral terms applies a multiplier on the level of temperature error. The Derivative term applies a multiplier on the rate of change in temperature error. When all three terms are added together, the result is the change in control output.
Contact #CICPittsburghLLC to help you with your process control and PID Loop tuning to optimize your zinc bath temperature control.